OR/17/002 Work Package 3: Experimental rock physics
Chadwick, R A. 2017. DiSECCS Final Summary Report. Work Packages 1 – 4 British Geological Survey Internal Report, OR/17/002. |
The original aim of WP3 was to take advantage of recent developments in the National Oceanography Centre (NOC) rock physics laboratory to investigate the effect of CO2/brine saturation on the seismic response of synthetic rock samples with aligned fractures. The observations would be used to inform the development of theoretical rock physics models in WP2 linking seismic P- and S-wave velocity and attenuation to CO2 saturation and the presence of fractures, their number density, size and orientation. The experiments were initially aimed at answering questions around the seismic detection of geotechnical effects in brittle formations prone to hydraulic fracture during CO2 injection, such as the highly cemented reservoir sandstones at In Salah, and the intermediately cemented reservoir sandstones at Snøhvit. However, due to the failure to obtain monitoring data from In Salah and following developments in other work packages, our priorities shifted towards experiments on the very weakly cemented sands at Sleipner. This presented a number of new technical challenges as the ultrasonic rig was designed primarily for rock samples. However additional financial investment from NOC, allowed us to completely redesign our experimental rig for simultaneous monitoring of geophysical (ultrasonic, electrical resistivity), geomechanical (stress-strain) and fluid transport (relative permeability) properties under realistic pressures and temperatures simulating CO2 injection. This has been a major achievement, producing the first comprehensive experimental datasets of this type (Falcon-Suarez et al, 2016).
A related NOC/University of Edinburgh collaboration sought to link fluid (air/water) saturation effects to rock physics models in fractured rocks, and those results are reported separately in the following publications: Amalokwu et al. (2016)[1]; Amalokwu et al. (2014)[2]; Amalokwu et al. (2015a)[3]; Amalokwu et al. (2015b)[4].
The work developed here has focussed on the distinction between pore fluid distribution and geomechanical effects during CO2-injection in Sleipner-like reservoirs. We have used synthetic sandstones as proxies of saline siliciclastic reservoirs and also real samples from the Utsira Sand at Sleipner to run a set of brine-CO2 flow-through tests. The tests replicate shallow reservoir conditions (~900 m depth) and simulate different stages of CO2-injection under hypothetical inflation/depletion scenarios.
The experiments were conducted with a new experimental rig for CO2 injection simulations that was specially designed and assembled at NOC during the first and second years of the project (2013–2015). The rig was designed to relate geophysical signatures of reservoir sandstones to their hydro-mechanical, thermal and geochemical responses during the co-injection of up to two fluids (brine and CO2), under realistic environmental and geological conditions.
Experimental methodology (Tasks 3.1 and 3.2)
Experimental rig
We have designed a new experimental rig for observing changes in geophysical, geomechanical and transport properties during flow tests of up to two fluid phases through a rock sample 5 cm in diameter, and 2.0–2.5 cm high, under realistic reservoir conditions (Figure 1).
The rig allows different configurations depending on the needs of the experiment. It is designed around a triaxial cell core holder for confining rock samples at pressures up to 69 MPa. The confining fluid (mineral oil) is delivered from a dual pumping controller (Teledyne ISCO model EX100D) that is configured in a non-coupled mode which allows the independent control of axial and radial confining pressures. Inside the vessel, a 6 mm wall, 190 mm high rubber sleeve isolates the core plug from the confining fluid. The rubber sleeve is perforated by 16 stainless steel electrodes for electrical resistivity tomography measurements. The wires from the electrodes are extracted from inside the pressure-vessel via feedthrough ports on the vessel-wall, and connected to an electrical resistivity tomography data acquisition system (North et al., 2013[5]). The system uses a tetra-polar electrode configuration to minimize electrode polarization artefacts. A total of 208 individual tetra-polar measurements (using various permutations of current injection and potential difference sensing electrode pairs) are acquired during each acquisition run. These data are then inverted using software based upon the EIDORS MATLAB toolkit (Andy & William, 2006[6]) for a uniform/homogeneous isotropic resistivity and heterogeneous isotropic resistivity distribution. Both inversion schemes employ a finite-element forward model of the sample and electrodes.
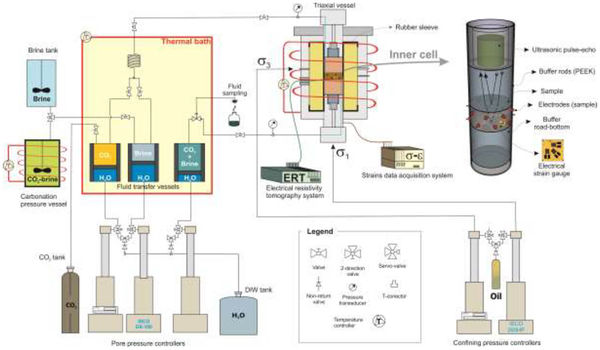
The sample is axially confined with two platens housing the ultrasonic pulse-echo sensors for measuring ultrasonic velocity and ultrasonic attenuation (Best et al., 2007[7]). These are indirectly in contact with the sample but with the two buffer rods in between. As shown by the 'inner cell' drawing (Figure 16), the core plug is isolated from the rest of the rig and the ultrasonic transducer by two PEEK buffer rods. The buffer rods have well-defined acoustic impedance and low energy loss, providing a reliable delay path to enable the identification of top/base sample reflections for calculating ultrasonic velocities (Vp and Vs) and attenuations (inverse quality factors Qp-1 and Q -1) using the pulse-echo technique (McCann & Sothcott, 1992[8]). The technique provides useable frequencies between 300–1000 kHz with absolute accuracies of ± 0.3% for velocity, and ± 0.1 dB cm-1 for attenuation (for 1” diameter single mode transducers). For the brine-CO2 flow-through tests (described below), we used dual P/S wave transducers which give accuracies of ± 0.3% for velocity and ± 0.2 dB cm-1 for attenuation (Best, 1992[9]). The buffer rods have built-in pathways (inlet and outlet ports) to conduct the pore fluid through the sample. The surfaces of the rods in contact with the sample are specially designed with a circumferential fluid flow pathway to facilitate fluid spreading upstream and fluid collection downstream.
The axial platens and access to the inner triaxial vessel are configured to allow the bypass of leads from strain gauges epoxy-glued to the side-wall of the sample. The leads are connected to a 4- channel data acquisition conditioner (Vishay-Model D4), which accepts either full-, half-, or quarter-bridge configuration for 120-, 350-, and 1000-ohm bridges. The pore pressure is controlled by three high-pressure, high-accuracy, pumping controllers: a dual Teledyne ISCO model EX100D, configured in separate mode for delivering two independent fluids, and a single controller Teledyne ISCO model ED100 acting as back pressure downstream of the sample. The pore fluids are indirectly supplied via fluid transfer vessels (FTVs) with the aim of preventing potential damage to the controller from corrosive fluids such as brine or CO2. Also, the FTVs allow heating of the fluids to target conditions by direct immersion in a tank made of PVC specially designed for temperatures up to 100ºC. The three vessels are connected to the three pumping controllers: two for delivering brine and CO2, and one for receiving the fluid, after passing through the sample, while setting the pore pressure constant. To further control the pore pressure, two piezo-resistive pressure transmitters (Keller model PA-33X) are located in the pipeline up- and downstream but very close to the sample, to accurately measure pressure drops and temperature changes during the test. An additional external carbonator-vessel is designed to prepare and store the CO2-saturated brine, for refilling the FTVs. The carbonator contains magnetic stirrers excited by a magnetic motor located underneath, and can be pressurized up to 30 MPa and heated up to 80ºC. The pipeline includes different ports both up- and down-stream of the sample for pore fluid sampling and geochemical analysis.
The triaxial vessel is also wrapped with an electrical rope heater connected to a PID (proportional/integral/derivative) controller (maximum temperature 150ºC; accuracy ± 0.5ºC) which sets the target temperature in the vessel according to the information received from an inner-vessel thermocouple. In addition, the load frame (containing the triaxial vessel and pipeline-pressure sensors) is enclosed in a commercial greenhouse cover system dotted with heat fans and automatic controllers to keep the temperature of the rig constant.
Samples
Experiments were carried out using synthetic sandstones and real samples of Utsira Sand, the storage reservoir at Sleipner. This section addresses the preparation and main physical properties of the samples used for the tests.
Synthetic sandstones
We prepared three synthetic sandstone specimens by mixing well-sorted coarse quartz-sand, kaolinite and silica cement at a specific ratio (Table 1), following the manufacturing process proposed by Tillotson et al. (2012)[10]. In all the cases, the mixture was then compressed in a 5 cm diameter stainless-steel mould, at the differential pressure conditions of a hypothetical 900 m depth CO2 storage reservoir. Finally, the pressurized mixture was oven-dried for one week, according to the manufacturing procedure.
Sample | Q-sand (wt.%) |
Kaolinite (wt.%) |
Si-cement | Φ | ρd g cm-3 |
kabs mD |
Synthetic-1 | 74 | 18 | 8 | 0.26 | 1.92 | ~1 |
Synthetic-2 | 86 | 11 | 3 | 0.45 | 1.47 | ~100 |
Synthetic-3 | 82 | 13 | 5 | 0.38 | 1.59 | ~50 |
After removal from the manufacturing mould, the resulting specimen was firstly flushed with de-ionised water to remove residual non-bounded particles from the porous medium. Then, ~2 cm length, 4.95 cm diameter samples were cut and ground in parallel within ± 0.01 mm. Porosity (f) was determined by helium porosimetry, and absolute permeability (kabs) to water (brine) was determined using the steady state method based on Darcy’s law for the whole range of differential pressures simulated in the subsequent flow-through tests. The value of kabs presented in Table 1 corresponds to those obtaining under starting-test conditions i.e. at maximum differential stress.
Utsira Sand samples
Samples from the Utsira Sand in the upper section (E641 - 1085–1085.25 m) of the well 15/9-A- 23, Viking Graben, Central North Sea, were used to perform brine-CO2 flow-through experiments. However, the available intact core material from this site was limited to trimmings of loose sand and a small piece of intact core (Figure 17).
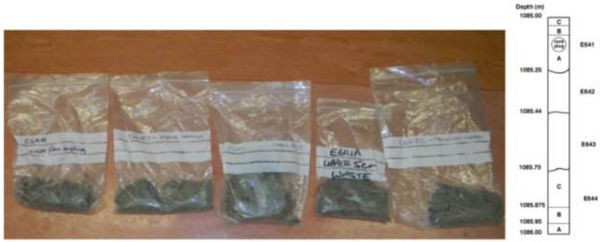
The samples were contaminated with drilling fluid, especially the outer parts of the core, which could condition the geophysical properties of the sample. Therefore, trimmings were washed for several hours prior to taking measurements; the weak grain-packing of the intact core sample led us to conduct the washing in the triaxial vessel (before running the experiment) to preserve the original structure of the rock.
Sample | Description |
Weight (g) |
E641B2 | Trimmings clean |
195.5 |
E641A | Upper 5 cm. Waste |
277.3 |
E641C | 1085–1085.35 |
595.2 |
E641B3 | Trimmings |
244.7 |
E641A | Waste from samplings |
248.3 |
Test configuration and methodology
Flow-through tests
We conducted five flooding tests using synthetic sandstones (three tests) and Utsira Sand samples (two tests; only one with CO2-brine fluids). In all cases, the experiments were steady-state drainage tests where electrical resistivity was used to determine the saturation changes in the porous medium.
The flow-through tests were configured to simulate hypothetical inflation/depletion scenarios on shallow-saline-siliciclastic reservoirs such as those in the North Sea. Specifically, we applied Sleipner-like conditions as the initial conditions of our tests: lithostatic confining pressure (sc) of 16.5 MPa and 7 MPa of pore pressure (Pp); temperature between 32 and 35˚C depending on the test (to be above the CO2 critical point of 31˚C and 7.39 MPa); sample (synthetic) saturated with degassed 35 g L-1 NaCl-brine (electrical resistivity ~0.19 Ω m).
Samples were saturated via imbibition under vacuum conditions. Once in the triaxial vessel the pore fluid was injected from the bottom end of the sample to remove any remaining air bubbles from the pore space, at a constant flow rate. To reach the target reservoir conditions of the starting point of the tests, the confining and pore fluid pressures were simultaneously increased whilst maintaining constant effective pressure (Peff = σc- Pp). After not less than two days of free compaction and settlement (geomechanical stabilisation), the samples were subjected to brine-flow between 0.25 to 0.5 ml min-1, while setting the pressure downstream to 7 MPa. Thereafter, an unload/loading sequence of effective pressures was reproduced by increasing the pore pressure downstream ~1 MPa stepwise from 7 MPa to 12 MPa and back to 7 MPa, while keeping the confining pressure constant at 16.5 MPa. For each step, a minimum of one pore volume (PV) was forced to circulate through the sample. Pore pressure up- and downstream and strains were continuously recorded, while at the end of each step, electrical resistivity and ultrasonic measurements were collected.
The brine-CO2 co-injection stage started after the first (100% brine) flooding sequence. The new solution injected into the sample was a mixture of brine and CO2 (with differential fractional flows) independently set by the corresponding pumping controller, but keeping the resulting total flow (Q) constant (Q = Qw + QCO2). The delivered fluids met at a certain point in the pipeline, flowing together thereafter for no less than one hour along pipe of 1.6 mm internal diameter before reaching the sample, which ensured the resulting brine-CO2 fluid was in equilibrium. In all the tests, this experimental procedure was repeated six times, varying 20% stepwise the fractional brine:CO2 flow up to 100% CO2, the final drainage stage. In two of the tests, an additional forced imbibition stage was simulated by flowing back 100% brine into the sample. Between two consecutive unload/loading sequences, the existing pore fluid was replaced by the new solution, which was forced to flow through the sample at the initial Pp of the sequence for no less than 4 PVs.
Electrical resistivity into degree of saturation
Archie’s law (Archie, 1942[12]) relates the degree of brine saturation (Sw) to the bulk electrical resistivity (ERb) of a rock through the connectivity of the porous medium and the electrical resistivity of the pore fluid (ERw):
where φ is the porosity, and a, m and n are empirical parameters for a particular rock, comprising the proportionality constant, cementation factor and the saturation exponent, respectively.
In our experiments, the initial stage is 100% brine saturation so that the initial bulk electrical resistivity (ER0) is reduced to:
Later on, the brine-CO2 co-injection implies partial saturations of both phases as Sw = 1- SCO2 , which can be can be obtained by dividing equation (1) by equation (2) Nakatsuka et al., 2010[13]):
Absolute and relative permeability
The absolute permeability to brine was calculated during the 100% brine flow stage of the experiments, for every Peff step, using the steady state flow method based on Darcy´s law:
where k is permeability, Q the volumetric flow rate, ΔP the pressure drop across the sample, A the cross sectional area, L the length, and μ the dynamic viscosity of the fluid.
Assuming a homogenous contribution of the whole cross sectional area to the flow through the entire core, the above expression can be modified for our two-phase brine-CO2 system in which the relative permeability of each phase (kr,i) is a function of the partial contributions to the total saturation:
where subscript i refers to each phase.
With the calculated relative permeabilities, we adjust the curves for each phase using the Brooks- Corey model (Brooks & Corey, 1964[14]) for a brine-CO2 two phase system (kr,w and kr,CO2):
where Nw and NCO2 are the Corey fitting-components for brine and CO2.
In our tests, the irreducible water saturation (Swr) is also a fitting parameter.
Strains
Sample deformation was measured by 350 W m 90° bi-axial strain gauges. Our first approach was to epoxy-glue the gauges onto the side-wall of the rubber sleeve, within the triaxial vessel, and to calibrate the signal using an aluminium sample of well-known deformation properties and the information from the axial piston displacement. However, sleeve deformation masked the radial deformation of the sample, so we modified the design of our triaxial vessel to allow extracting the wires of strain gauges epoxy-glued directly onto the side-wall of the sample.
As a result, after the first test (Falcon-Suarez et al., 2016[15]) axial (εaxε) and radial (εr) strains were measured continuously during the whole test, allowing the monitoring of the volumetric deformation (εv) of the sample (i.e. relative changes of porosity) according to the following expression:
Results (Task 3.3 ad 3.4)
Synthetic sandstones
Figure 18 shows the results of the first test conducted on synthetic sandstone as presented in Falcon-Suarez et al. (2016)[15]. In this contribution, we presented our novel experimental approach for understanding the geophysical and hydrodynamic responses of reservoir sandstones under CO2 injection. It was our first set of experimental data using the new setup for a CO2/brine flooding test through synthetic sandstone, simulating a shallow, low permeability CO2 storage reservoir. We measured simultaneously ultrasonic P- and S-wave velocities and attenuations, electrical resistivity (including tomography), axial strain and relative permeability for variable brine:CO2 flow rates and differential stress conditions. Our results showed that it is possible to distinguish between geomechanical and pore-fluid effects on the measured elastic wave and electrical properties.
Similar data were obtained during the tests performed on synthetic samples 2 and 3, and the analysis and interpretation of results will be presented in coming contributions. For synthetic sample 2, the first test was repeated to study the effects of the injection on an anomalously high porosity medium. For synthetic sample 3, the experiment is particularly interesting because the porosity of the sample and the experimental conditions are similar to those estimated for Sleipner. Furthermore, we analyse the significance of geomechanical variations triggered by the injection of CO2 in our rock sample during a brine-CO2 flow-through test with respect to those associated to the natural recharge of the aquifer after ceasing the injection activities. The data suggest very little damage due to CO2-aquifer interaction and potential brine-induced effects during the natural recharge of the aquifer after the cease of CCS activities (Falcon-Suarez et al. 2018[16]).
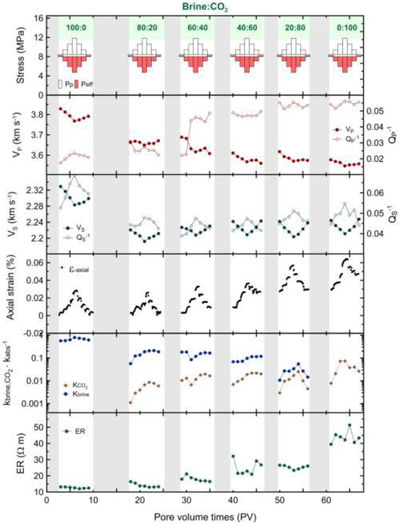
Utsira Sand samples
The first sample, made from trimming fragments of loose sand, was subjected to the first unloading/loading 100% brine flow-through sequence applied on the rest of the tests. The results were presented in Falcon-Suarez et al. (2015)[17]. However, a number of issues arose when the brine-CO2 co-injection stage started and the results are therefore limited to brine flow (Figure 19).
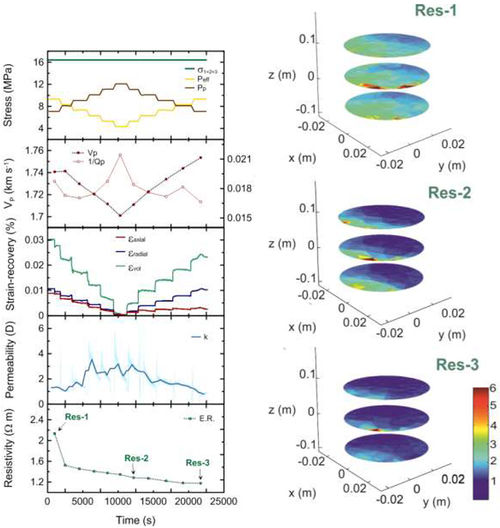
Our second experiment was carried out using an intact core sample from the Utsira Sand. In this case, the sample was particularly prepared for allowing brine-CO2 co-injection while measuring deformation and geophysical signatures. However, such a careful sample preparation impeded relative permeability determinations. Furthermore, in this case, the ultrasonic wave velocities and attenuations were limited to P-waves. Analysis and interpretation of results will be presented in upcoming contributions
Conclusions
We have contributed new laboratory experimental capability and methods for realistic simulation of CO2 reservoir injection, geomechanical and geophysical monitoring in reservoir rock samples. Moreover, we have produced the first comprehensive datasets of sand/sandstone responses to CO2 injection that are worthy of further analysis and useful for generic geomechanical/seismic model development.
The new NOC experimental capacity has opened up new opportunities for further experimental runs aimed at reproducing the response of specific reservoir types. These could be addressed either by obtaining actual core samples, or by further development of our synthetic rock manufacturing methods. One issue is the wealth of data produced by the experimental runs to date. We have only just started to analyse these data in any great detail, and are now feeding the results across to Work Packages 1 and 2 and to follow-on modelling studies. In separate projects, we are developing acoustic frequency range measurements on sands and overburden sediments/rocks during CO2/brine injection for informing well logging and high resolution seismic remote sensing for sub-sea CO2 storage monitoring.
References
- ↑ Amalokwu, K, Best, A I, & Chapman, M. 2016. Effects of aligned fractures on the response of velocity and attenuation ratios to water saturation variation: a laboratory study using synthetic sandstones. Geophysical Prospecting 64, 942–957.
- ↑ Amalokwu, K, Best, A I, Sothcott, J, Chapman, M, Minshull, T, & Li, X-Y. 2014. Water saturation effects on elastic wave attenuation in porous rocks with aligned fractures. Geophysical Journal International 197, 943–947.
- ↑ Amalokwu, K, Chapman, M, Best, A I, Minshull, T A, & Li, X-Y. 2015a. Water saturation effects on P-wave anisotropy in synthetic sandstone with aligned fractures. Geophysical Journal International 202, 1088–1095.
- ↑ Amalokwu, K, Chapman, M, Best, A I, Sothcott, J, Minshull, T A, & Li, X-Y. 2015b. Experimental observation of water saturation effects on shear wave splitting in synthetic rock with fractures aligned at oblique angles. Geophysical Journal International 200, 17–24.
- ↑ North, L, Best, A I, Sothcott, J, & MacGregor, L. 2013. Laboratory determination of the full electrical resistivity tensor of heterogeneous carbonate rocks at elevated pressures. Geophysical Prospecting, 61, 458–470.
- ↑ Andy, A, & William, R B L. 2006. Uses and abuses of EIDORS: an extensible software base for EIT. Physiological Measurement 27, S25.
- ↑ Best, A I, Sothcott, J, & McCann, C. 2007. A laboratory study of seismic velocity and attenuation anisotropy in near-surface sedimentary rocks. Geophysical Prospecting 55, 609–625.
- ↑ McCann, C, & Sothcott, J. 1992. Laboratory measurements of the seismic properties of sedimentary rocks. Geological Society, London, Special Publications 65, 285–297.
- ↑ Best, A I. 1992. The prediction of the reservoir properties of sedimentary rocks from seismic measurements. University of Reading, 393 pp.
- ↑ Tillotson, P, Sothcott, J, Best, A I, Chapman, M, & Li, X-Y. 2012. Experimental verification of the fracture density and shear-wave splitting relationship using synthetic silica cemented sandstones with a controlled fracture geometry. Geophysical Prospecting 60, 516–525.
- ↑ Pearce, J, Kemp, S J, Bouch, J, Turner, G H, & Steadman, E J. 2002. A petrographic study of the Utsira Formation and its reaction with CO2-rich fluids during hydrothermal experiments. British Geological Survey Commissioned Report CR/02/071, 62 pp.
- ↑ Archie, G E. 1942. The electrical resistivity log as an aid in determining some reservoir characteristics. Transactions of the American Institute of Mining, Metallurgical, and Petroleum Engineers 146, 54–62.
- ↑ Nakatsuka, Y, Xue, Z, Garcia, H, & Matsuoka, T. 2010. Experimental study on CO2 monitoring and quantification of stored CO2 in saline formations using resistivity measurements. International Journal of Greenhouse Gas Control 4, 209–216.
- ↑ Brooks, R H, & Corey, A T. 1964. Hydraulic properties of porous media. Hydrology Paper 3. Colorado State University, Fort Collins 27.
- ↑ 15.0 15.1 15.2 Falcon-Suarez, I, Best, A, North, L, & Browning, F. 2016. Nondestructive assessment of static and dynamic geomechanical properties of sandstone samples for geological CO2 storage monitoring. SEG Technical Program Expanded Abstracts 2016, pp. 3231–3235.
- ↑ Falcon-Suarez, I, Papageorgiou, G, Chadwick, A, North, L, Best, A, & Chapman, M. 2018. CO2-brine flow-through on an Utsira Sand core sample: experimental and modelling. Implications for the Sleipner storage field. International Journal of Greenhouse Gas Control, 68 (2018), 236–246.
- ↑ 17.0 17.1 Falcon-Suarez , I, North, L, & Best, A. 2015. Geophysical and Hydro-Mechanical Coupled Monitoring for Efficient Control of CO2 Storage. In: 3rd International Workshop on Rock Physics, Perth. http://3iwrp.org/submissions/abstracts/AB_LN20141212-RAD55CE9.pdf